Vidrala, el titán de los envases de vidrio.
Un sistema que alinea equipos, personas al frente de la transformación y un liderazgo operacional.
Castellar Vidrio, es la fábrica que el grupo Vidrala tiene en Europa, formando parte del gigante alavés de fabricación de envases de vidrio. Con plantas de producción en España, Portugal, Reino Unido, Irlanda y Brasil, la empresa destaca por su presencia global y su compromiso con la calidad y la innovación en la industria del vidrio.
La compañía actualmente es capaz de ofrecer un portfolio de más de 100 modelos de botellas de vidrio en 6 colores diferentes y con una capacidad productiva de entre 400 y 500 millones de unidades anuales. A nivel grupo, estamos hablando de una capacidad de 9.300 millones de envase al año. Con estos volúmenes de producción, son capaces de satisfacer las diversas necesidades en múltiples industrias, desde alimentos y bebidas hasta productos de cuidado personal.
La planta de Castellar del Vallés que cuenta con un equipo de 250 empleados tiene un compromiso firme con la calidad y la sostenibilidad que les posiciona como un socio estratégico para quienes buscan envases eficientes, estéticos y funcionales.

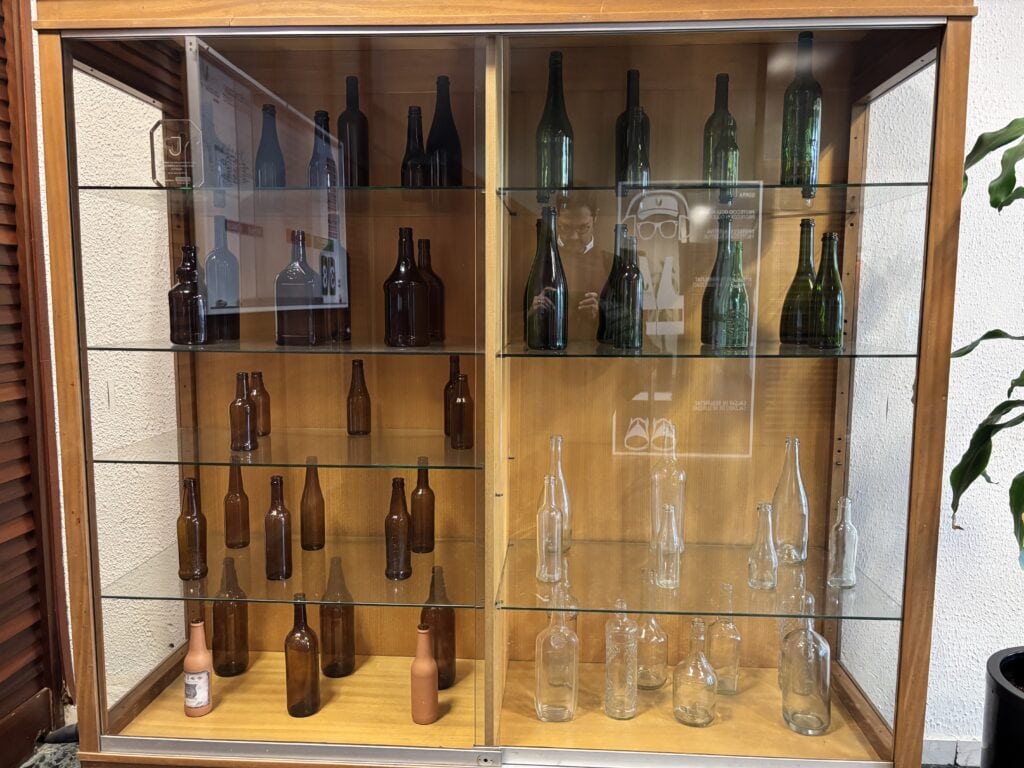
Hablemos de ti ¿quién es Marc Bertran?
De formación soy biotecnólogo, pero llevo enamorado del Lean Manufacturing y la mejora continua desde hace más de 15 años.
Actualmente llevo casi 6 años en la planta que el grupo Vidrala tiene en Castellar del Vallès. Anteriormente he ejercido de responsable de mejora en compañías como Codorníu o Mango y estuve ejerciendo de consultor de operaciones un periodo de tiempo.
Además de mi background operativo e industrial, también compagino mi trabajo en la docencia, en un programa de Lean Six Sigma Green Belt en LaSalle.
Siempre he estado vinculado a la excelencia operacional en todas las empresas con las que he trabajado por mi convicción de la excelencia.
Ya conocemos lo que es el Lean Manufacturing y la Excelencia Operacional, pero dime ¿cómo Vidrala ha traducido la teoría a la realidad? ¿cuáles son los principales ejes o palancas del sistema de excelencia operacional de vidrala?
Para Vidrala y el grupo, la excelencia en las operaciones la explicamos a través de nuestro Vidrala Operating System (VOS) y sus cinco ejes de desarrollo que establecen unas dinámicas y formas de trabajo basadas en metodologías de gestión eficiente y que nos permiten alcanzar los resultados operativos y financieros.
Más allá de cómo entendemos la excelencia, tenemos claro que las personas son el eje conductor y que, hay que crear esa participación e implicación en todos los niveles jerárquicos.
Volviendo a nuestro sistema de mejora, seguramente el Relentless Loss Elimination (Eliminación de Pérdidas de Producción) es el eje con mayor impacto en la excelencia operativa de Vidrala.
Es el pilar que llevan en el ADN todas las personas que trabajan en el área industrial de Vidrala. Tenemos que pensar que la industria del vidrio es un proceso continuo non-stop, lo que significa que opera 24/7 ininterrumpidamente y que el flujo del vidrio está constantemente “cayendo”. Esto hace que cualquier incidencia de producción sea necesario solucionarla al momento. No existe la posibilidad de “cerrar el grifo”.
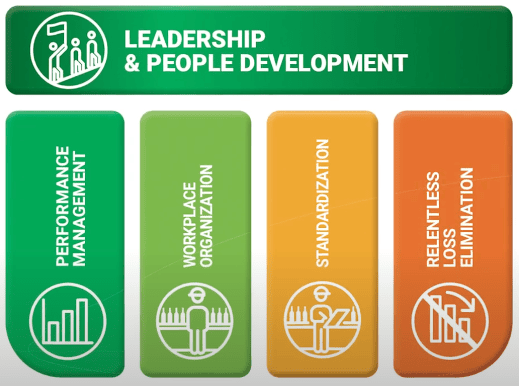
Dentro de vuestro sistema continua, ¿serias capaz de detectar qué metodologías consideras que tienen mayor retorno en vuestra planta?
En una planta industrial con un recorrido de pocos años en la mejora continua y la excelencia operacional, las 5S y el WPO (WorkPlace Organitzation) como llamamos internamente son, hoy en día, los métodos a implantar y seguir desarrollando.
Aunque el retorno de un proyecto 5S es difícil de calcular a nivel económico, el impacto a nivel cultural sí que se aprecia tanto en áreas productivas cómo de talleres.
Actualmente, las 5S, como parte fundamental de nuestro pilar Standarization, forman parte del ADN de cualquier persona que entra a nuestro equipo. Tras tiempo, hemos conseguido integrar en las personas que no se puede construir un camino de mejora continua sin asegurar un nivel alto de orden, limpieza y estandarización.
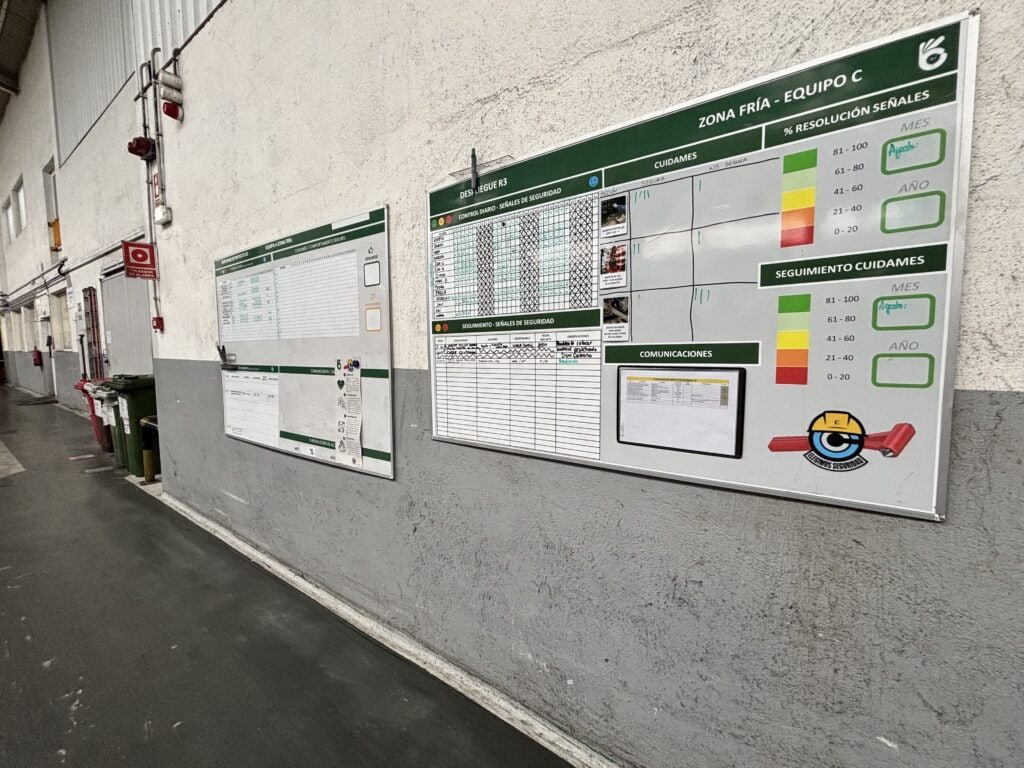
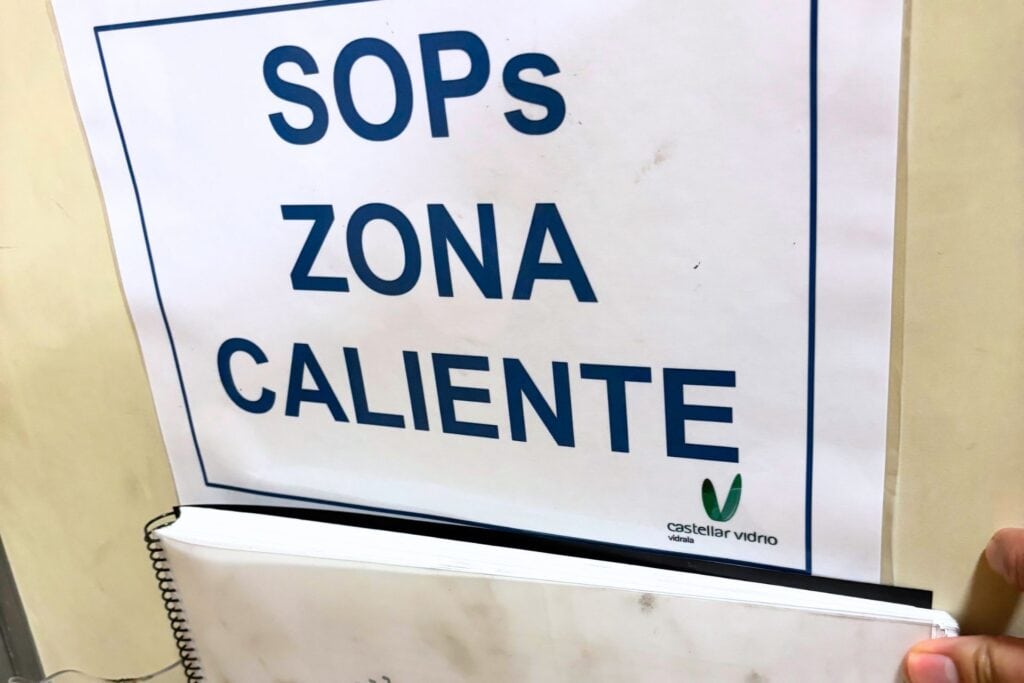
En este sentido, las 5S no solo contribuyen a mantener un entorno de trabajo ordenado y estandarizado, sino que suponen la base de nuestra forma de trabajo y son una palanca fundamental para la prevención de riesgos laborales, ya que reducen las posibilidades de accidentes y fomentan una cultura de seguridad en la planta.
No es un camino fácil. Cuando de persona se trata y a pesar que la seguridad parece un tema obvio, hay que trabajar de forma constante y continua la comunicación, involucración, formación y desarrollo en materia de prevención de accidentes.
Contamos para ello con ciertos elementos visuales que, sumados a la estrategia que el propio equipo de seguridad tiene, ayudan a avanzar paso a paso hacia unos niveles excelentes en términos de seguridad laboral.
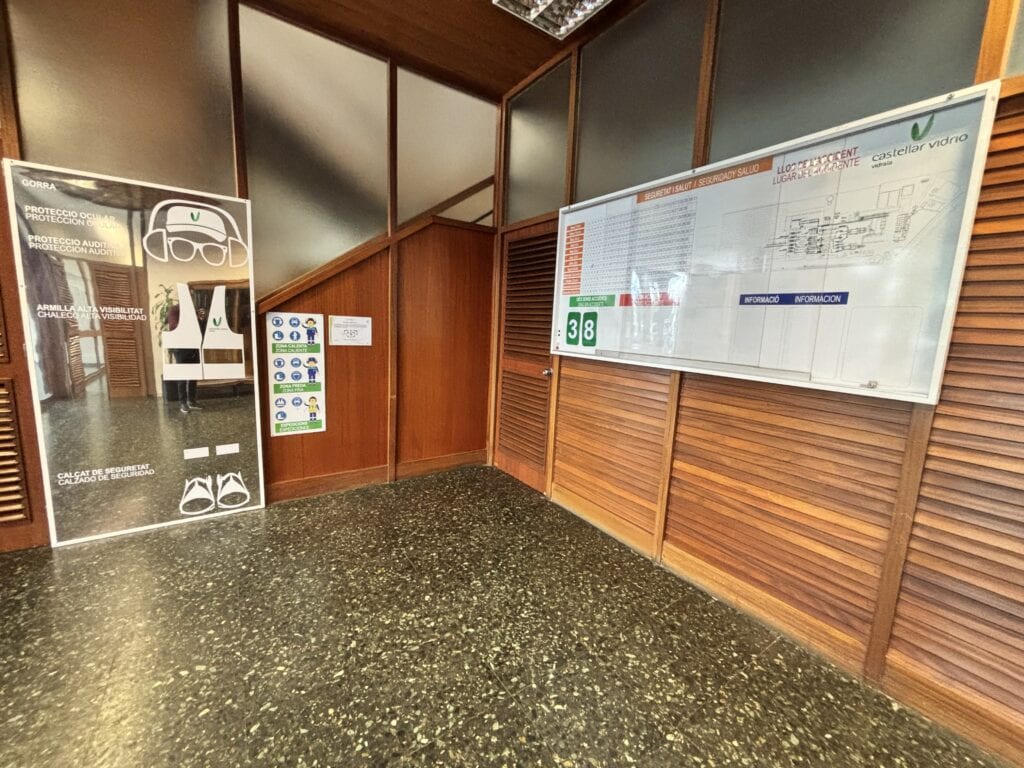
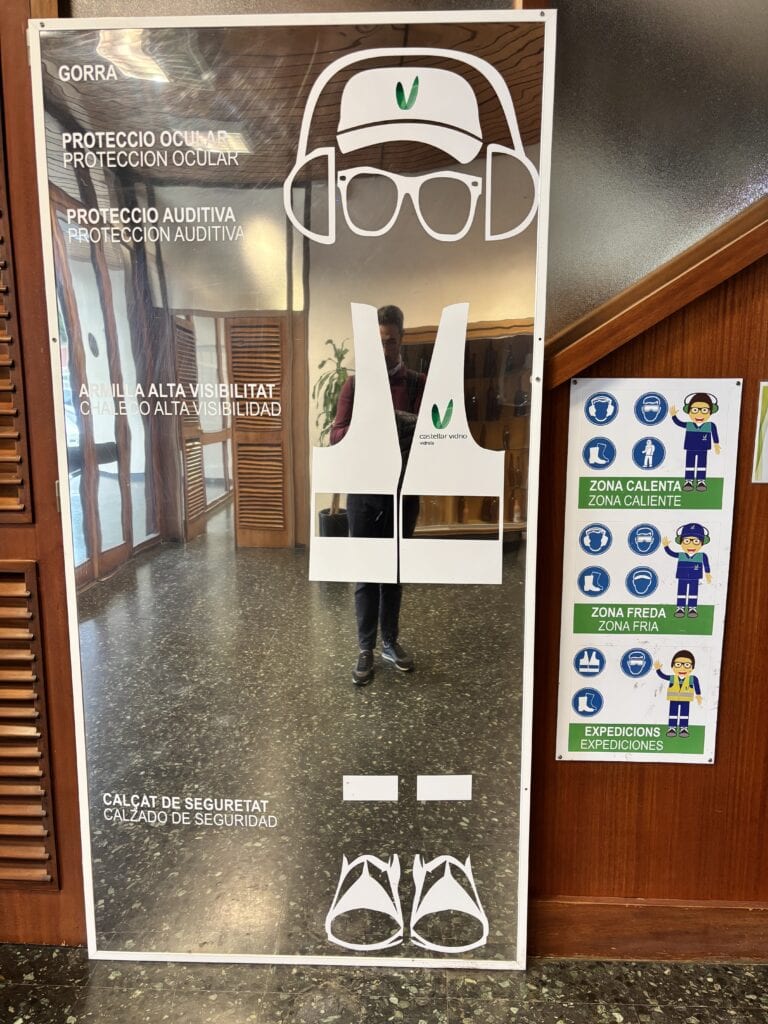
Cuentanos Marc ¿Cómo gestionáis la transformación de la planta en términos de excelencia operacional?
Actualmente, las dinámicas que impulsan la excelencia operacional (OPEX) en la planta se dividen en dos grandes categorías:
- Gestión del portfolio de proyectos estratégicos:
Este portafolio engloba un conjunto de actividades, reuniones y dinámicas orientadas a los proyectos de mejora de la planta. Constituye un foro quincenal donde se revisa el progreso del «Improve the Business», abordando iniciativas de corto y medio plazo en todas las áreas de la planta. Estas iniciativas se estructuran en torno a tres pilares fundamentales: sostenibilidad, competitividad y nivel de servicio. - Proyectos de corta duración:
Son iniciativas específicas que, generalmente, tienen una duración de una o dos semanas. Estos workshops están diseñados para gestionar tareas puntuales, como reparaciones o la coordinación de cambios de color en los hornos. Estos workshops comnparten una serie de características clave: por un lado requieren una coordinación diaria, implican la participación multidisciplinar de diversas áreas, su operativa supone una gestión de empresas contratadas externas y, por último, son trabajos en diferentes áreas de planta.
La ejecución de estas iniciativas se gestiona mediante herramientas visuales como pizarras Kanban, ciclos de trabajo en sprints y metodologías ágiles, que incluyen dailys para asegurar la coordinación del equipo. Este enfoque estructurado permite un soporte visual común del proyecto, seguimiento continuo, alineación de esfuerzos y rápida resolución de problemas.
¿Cómo es el día a día en la planta de Vidrala de un responsable de excelencia operacional? ¿A qué se dedica?
La posición de opex maanager en Vidrala combina una parte de función operativa y una parte de función estratégica. Desde la gestión de proyectos de eficiencia energética, a liderar una reunión de gestión de proyectos estratégicos de planta o implementando las 5S en un taller de mantenimiento.
A primera hora de la mañana, todos participamos en la reunión diaria de coordinación, donde se revisa la producción del día anterior y se coordinan las tareas del día en curso. A partir de ahí, cada día es completamente diferente.
Marc, me hicieron mucha gracia dos palabras habituales en vuestra jerga del vidrio, la primera es “la gota” y la segunda es el” chupa-chup”. ¿Qué son para vosotros estos conceptos?
La gota es el flujo de vidrio que mandamos desde los canales de los hornos a la máquina, al estar en dos niveles diferentes, se manda este flujo con unos punzones y unos agujeros en forma de gota hacia la máquina de moldeo.
Es una parte del proceso muy bonita por la rapidez y las condiciones de la operación. Debemos tener en cuenta que la gota cae 1100ºC
Todos los que somos de Castellar o de los pueblos de alrededor conocemos la fabrica del vidrio y el famoso chupachup. El chupachup es el antiguo deposito de agua antiincendio que daba respuesta a una necesidad de manera muy ingeniosa. Es un deposito de agua antiindencio alzado a 30 metros, de manera que aprovechando la energia potencial de la altura del agua, podemos llegar a toda la fabrica con presión pero si necesidad de ninguna bomba.
Lo del chupachup obviamente viene por la forma que tiene 😊 como se aprecia en la foto.
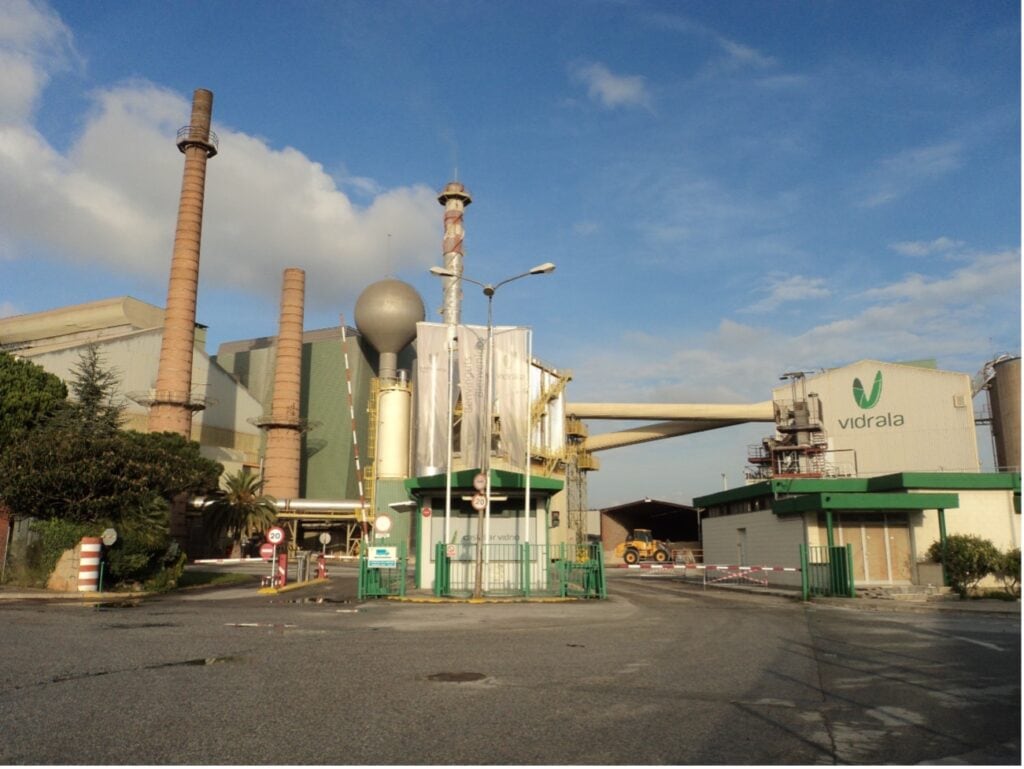
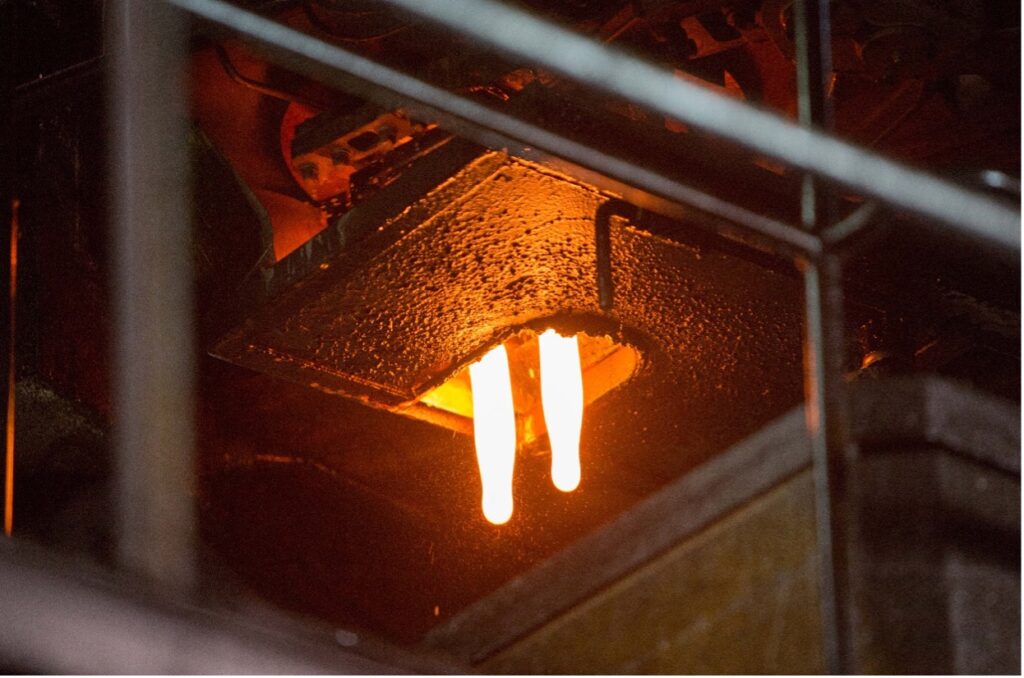
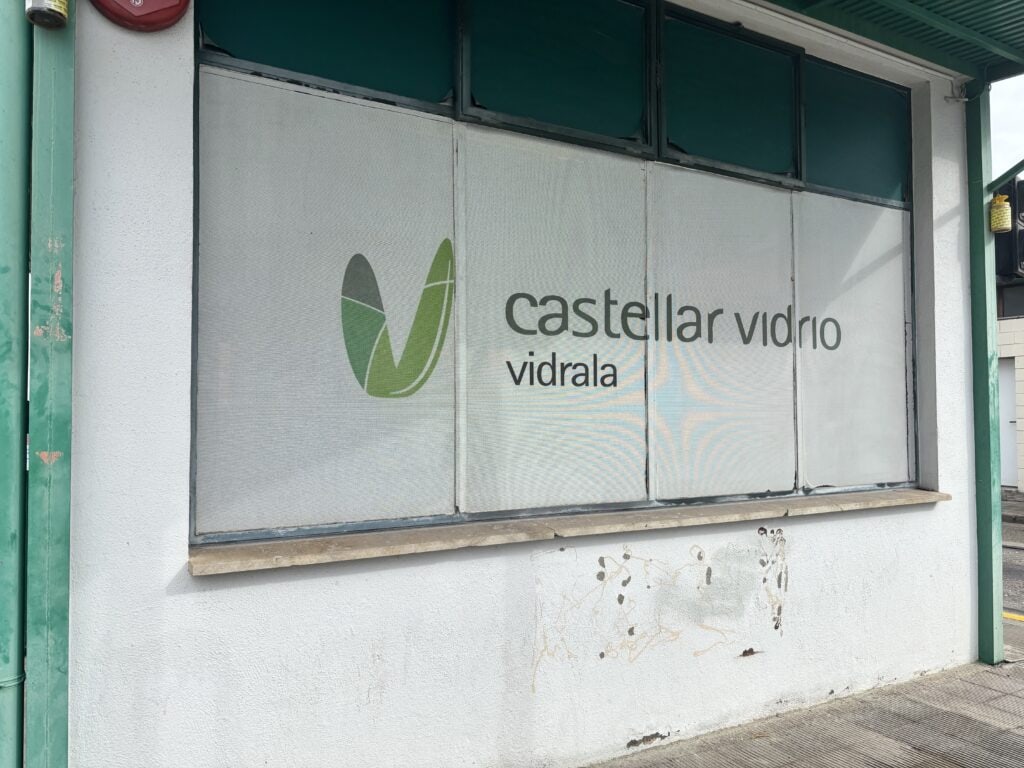
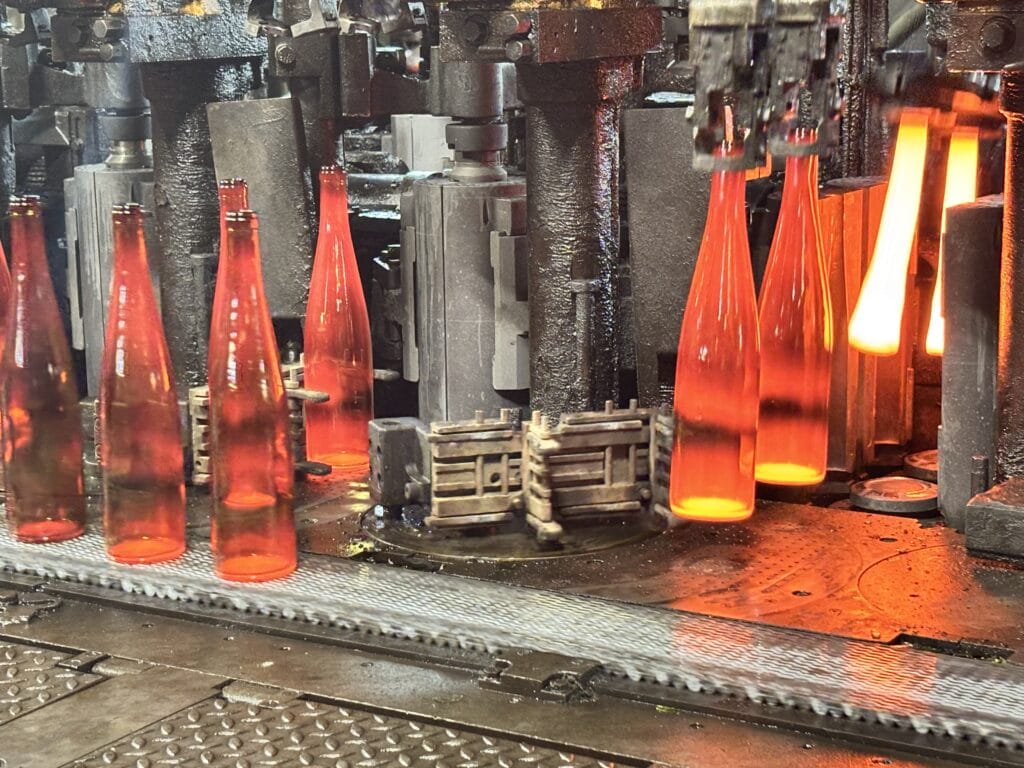